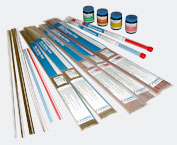
|
Stainless Steel Brazing
Stainless steel is a general term covering a group of
materials, which have different corrosion and heat resistant
properties dependent upon their composition and heat
treatment. Most users appreciate this difference but
there are still instances where drawings will merely
state 'stainless steel', All stainless steels can usually
be classified into groups that are collectively known
as Ferritic, Martensitic, and Austenitic steels
Ferritic Stainless Steels
The ferritic steels contain 12-18% chromium with up
to 0.5% nickel, and are magnetic. Their properties cannot
be improved by heat treatment and they rely on mechanical
working for their strength.
These steels, often referred to as stainless irons,
can be fabricated and present few problems in welding
although they can give difficulties in brazing. Common
applications are turbine blades and household cutlery
British Standard alloys of type 403 and 430 are included
in this group of steels.
Martensitic Stainless steels
These steels are heat-treated and consequently the effects
of temperature can influence the mechanical and corrosion
resistant properties. It is sometimes necessary to localise
the heat affected zone or heat treat the assembly after
joining. Martensitic steels are magnetic.
High chromium stainless steels are more affected by
temperature and consequently care must be taken to ensure
that the correct heat treatment is employed, either
before or after joining. Common applications are valve
holders and seatings, and surgical instruments where
sharp edges are required.
Austenitic Stainless Steels
The Austenitic steels are based on the 18% chromium
8% nickel composition although the chromium addition
can vary from 15-22% and the nickel from 6-11%. These
steels cannot be hardened by heat treatment and must
rely for their mechanical properties on mechanical working.
This means that any thermal joining treatment will reduce
the mechanical properties in the 'heat affected zone'.
Austenitic steels if heated between 55O °C and
750 °C will precipitate complex chromium carbide.
This will render the material susceptible to a rapid
corrosion process known as weld decay. The degree
of this precipitation will be a function of the carbon
content but it is obvious that most thermal joining
processes will be a potential hazard. The steels
can be stabilised by the addition of either niobium
or titanium and all Austenitic steels that are to
be brazed or welded should either be in this condition
or have a low carbon content.
Alloys include types 302, 303, 304, 310, 316, 321, 325
and 347.
ALLOY
|
Resistance
to Crevice Corrosion
|
Ferritic/Austenetic
|
Martensitic
|
SilBRAZE
56IN
|
YES
|
YES
|
SilBRAZE
55
|
NO
|
NO
|
SilBRAZE
40
|
NO
|
NO
|
SilBRAZE
60
|
In
some cases
|
In
some cases
|
Stainless steel is used for many applications where
it is subjected to stress and it is also frequently
subjected to a corrosive environment.
Strong ductile joints can be easily made on stainless
steel but care must be taken in the choice of brazing
alloy and grade of stainless steel to ensure that the
joint will be satisfactory in service. Brazing will
involve heating the steel to a temperature where carbide
precipitation (weld decay) would take place. It is therefore
essential that the steel must be stabilised, or low
carbon content steel is used.
Particular care must be taken in the selection of brazing
alloys for stainless steel when the resultant joints
are to be exposed to water or humidity in service. In
these conditions failure of the joint can result from
corrosion, often referred to as "interfacial or
crevice corrosion", at the brazing alloy/stainless
steel interface.
The mechanism of this failure is complex but the basic
mechanism is that a galvanic will be set up between
the brazing alloy and stainless steel that causes attack
along the interface between the two materials. Joint
failure is such that the brazing alloy can be detached
from the stainless steel. Where the brazing alloy has
been removed the surface of the stainless steel is usually
dull grey suggesting that the brazing alloy has failed
to wet and bond successfully. Failure due to crevice
corrosion is rare in joints made in austenitic stainless
steel but is more common in the low nickel or nickel-free
chromium steels of the Ferritic or Martensitic type.
Special brazing alloys have been developed to overcome
this problem. The most suitable silver brazing alloy
for service with any stainless steel where crevice corrosion
is a problem is a silver-copper- indium-nickel alloy
known as SilBRAZE 56IN. Being free of zinc, it is immune
to dezincification.
Other alloys that are less resistant to crevice corrosion
are also available.
Fluxes
The use of a flux is essential when brazing stainless
steel in air. With components where the joint area can
be easily heated up to brazing temperature, Easyflo
flux can be used. However, should prolonged heating
be necessary, a flux metal reaction will take place
when this flux is used. This reaction will form a film
on the surface of the stainless steel so that it cannot
be 'wetted' by the brazing alloy, and the addition of
fresh flux will not remove this film. In these instances
it is necessary to use Tenacity Flux No 5 flux. This
has improved high
temperature properties and does not react with stainless
steel. The only problem is that the residues are not
water-soluble and have to be removed with caustic soda,
or mechanical methods, such as grit blasting.
Fluxes containing boron, such as Tenacity 5A and Tenacity
6 should not be used where crevice corrosion is a known
service hazard.
Heating Methods for Silver Brazing of Stainless Steel
For silver brazing operations in air, hand torch or
fixed burners and induction heating are the most commonly
used heating methods.
|
|
|
|
|