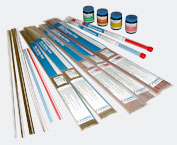
|
The High Silver SilBRAZE Series
The alloys in this series represent general purpose
alloys that can be used for brazing of low carbon and
low alloy steels, copper and most copper alloys, nickel
and nickel alloys, stainless steels (Refer Technical
Information), tungsten carbide (Refer Technical Information).
All the SilBRAZE alloys are cadmium free and pose very
little health hazards in their use.
Fluxes required for all the above brazing applications
and AGR Matthey fluxes are available for these purposes
in the form of powders or pastes. Selection of the appropriate
flux is based on matching the active range of the flux
to the melting range of the filler metal – the
flux has to be active at temperatures below the solidus
of the filler metal and must remain active at least
50C above the filler metal liquidus. Flux-coated rods
are also available in most of the alloys.
The alloys with melting ranges (difference between liquidus
and solidus) greater than 50°C generally are suitable
for filling larger gaps and forming large fillets, the
ones with a shorter melting range (generally also quick
flowing) are suitable for narrow, well-controlled joint
gaps, forming neat joints with small fillets. The alloys
with more than 55% silver are generally silvery in colour
and provide a good colour match for stainless steel
and nickel silver.
GENERAL PURPOSE
ALLOYS
|
SPECIAL
ALLOYS
|
SHORT MELTING
RANGE
|
LONG MELTING
RANGE
|
SILBRAZE 56
SILBRAZE 55
SILBRAZE 45
|
SILBRAZE 40
SILBRAZE 39
SILBRAZE 34
SILBRAZE 30
|
SILBRAZE 56IN (Stainless steels)
SILBRAZE 49 (Tungsten carbides)
SILBRAZE 49LM (Tungsten carbides)
|
CAUTIONS:
1. These alloys are not suitable for brazing low melting
metals eg magnesium, aluminium alloys
2. Copper alloys containing more than 2% aluminium require
special fluxes
3. For brazing stainless steels, please refer to Technical
Data for stainless steel brazing.
4. Joints made using brazing alloys containing tin must
not be quenched after brazing from temperatures over
300°C and are not recommended for joining materials
with large differences in coefficients of thermal expansion.
5. The maximum continuous operating service temperatures
of brazed assemblies using these alloys must not exceed
200°C.
|
|
|
|
|