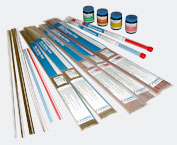
|
The SilBRAZE P Series Self-Fluxing Alloys for Copper Brazing
These alloys can wet copper in air without a chemical
flux. The mechanism of self-fluxing is a complex, two-stage
process:
- on melting, the brazing alloy dissolves the copper oxide
film on copper,
- the dissolved oxides subsequently react with the phosphorous
component of the alloy to produce a fusible copper meta-phosphate
slag on the surface of the molten brazing alloy.
The primary function of the slag is to protect the molten
brazing alloy from excessive oxidation during the brazing
cycle although it will dissolve some pre-existing copper
oxide.
For best results, the brazing rods should be as free of
surface oxides as possible prior to commencing brazing
otherwise a significant proportion of the phosphorous
is used up to scavenge the oxide on the rods to the detriment
of the work piece, leading to poor wetting. Also when
brazing large assemblies involving prolonged heating,
the brazing alloy itself can get oxidised during heating
as the self fluxing action of phosphorous is effective
only once molten. In such cases, use of additional flux
is advised.
The greyish coloured residue of the slag left on the work-piece
and the brazing alloy fillet does not subsequently cause
corrosion and need not be removed. When a tenacious green
residue is present after brazing this is a sign of excessively
long brazing cycles, which have led to flux exhaustion.
All these alloys have long melting ranges and with slow
heating rates can suffer liquation. Since used almost
exclusively on copper, which has high thermal conductivity,
the required high heating rates are best achieved with
oxy-acetylene or oxy/natural gas hand-torch heating.
Joint gaps should be 0.05-0.125mm, in some cases up to
0.2mm, gaps larger than this can create problems.
When used to braze brass or bronze, conventional borate
fluxes have to be used as phosphorous does not dissolve
zinc or tin oxide.
CAUTION
These alloys are not for use on high nickel alloys, nickel
or ferrous base materials due to the formation of brittle
phosphides.
These alloys are not suitable for use in sulphur atmospheres
especially at elevated temperatures. Maximum continuous
service temperature is limited to 200°C. At higher
temperatures, selective oxidation of the phosphorous in
the alloy occurs, with consequent deterioration of the
joints.
Joints brazed with these alloys are not suitable for continuous
sea-water exposure due to risk of selective dissolution
of phosphorous-rich micro phases.
|
|
|
|
|